November 2022
Amburn reaches conclusion of Phase 1 feasibility study with Final Public Report
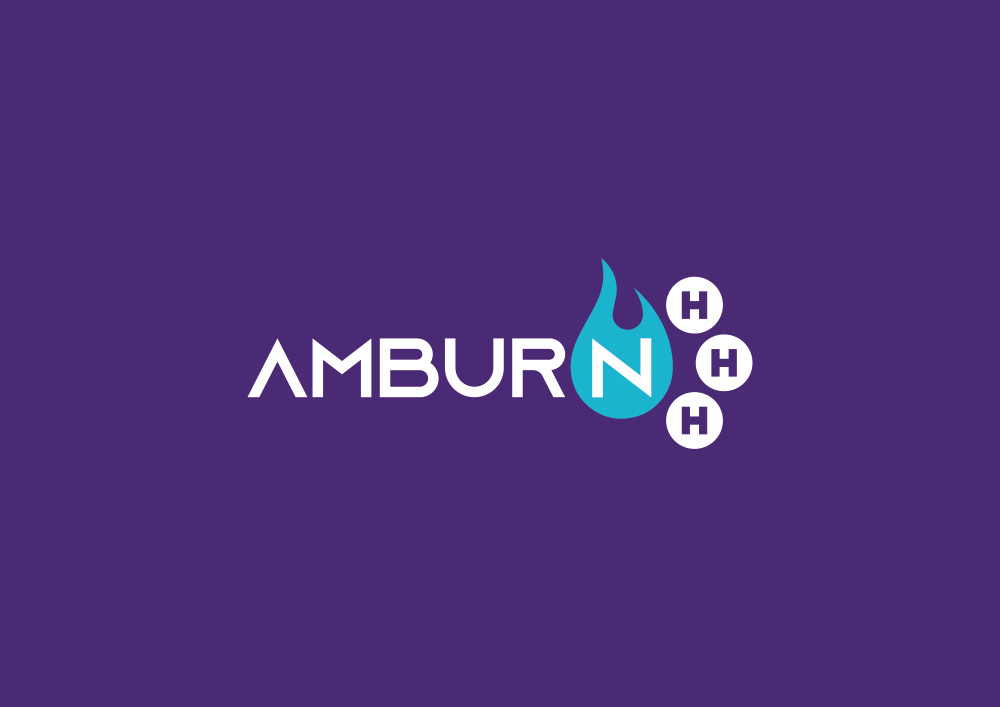
Phase 1 of the Amburn project concluded in November 2022, with the Amburn consortium undertaking a feasibility study into the viability of ammonia combustion as a low carbon solution for off-grid industrial heating, as part of the UK Government’s Industrial Fuel Switching Competition.
Technical barriers in the combustion of ammonia have meant that ammonia boilers are not yet available on the market. Project Amburn Phase 1 has begun to remove these barriers, and has shown that ammonia fuelled boilers are technical possible, commercially attractive, and safe as an option to decarbonise off-grid industrial sites.
The study showed that, from an economic perspective, ammonia-fuelled boilers have significant advantages over other low carbon solutions:
- Hydrogen struggles to compete with ammonia on a total cost of ownership basis, as it requires very low temperatures (-253oC) or high pressures (>500 bar) to achieve reasonable volumetric energy density. This, along with the relative lack of hydrogen distribution infrastructure, causes storage and distribution costs to be exceedingly high, particularly for sites located in remote places and/or utilising >10 days of back-up storage, as is common for many off-grid sites.
- Biofuels may offer an attractive transitional solution for off-grid heating, however competition from higher value sectors such as aviation and plastics for a finite sustainable biomass resource, means that they likely do not offer a long-term, scalable solution.
- Direct electrification requires significant grid upgrades, which can be costly and has long lead times.
- Heat pumps are a viable alternative to ammonia-fuelled boilers, however, low coefficient of performance for high temperature operations (>150oC) makes them more suitable for low temperature applications, such as domestic heating.
As well as proving commercial viability, the study removed some of the technical barriers currently preventing ammonia burners from entering the market. The consortium developed an innovative design capable of addressing the two key challenges associated with ammonia combustion:
- Low flame speed and flame stability: Ammonia has a lower burning velocity than hydrocarbon fuels, which can lead to unreliable ignition and unstable combustion. The Amburn design mitigates this by integrating an ammonia cracker unit inside the combustion chamber. The ammonia cracker decomposes a fraction (5% by mass) of the ammonia to produce highly flammable hydrogen (and nitrogen). The resultant fuel mixture has a flame speed of a similar order to fossil fuels (e.g., propane). This was proven by laboratory tests at Cardiff University for a small-scale prototype system at 25 kW.
- NOx emissions: Ammonia combustion has the possibility of increased NOx emissions, primarily from the presence of nitrogen atoms in the ammonia molecule (‘fuel NOx’). Testing at Cardiff University’s laboratory suggested that NOx emissions are minimised when ammonia is burned rich. However, rich burning leads to ammonia slip, which both wastes fuel and is dangerous, as ammonia is toxic at very low concentrations. Therefore, the Amburn burner utilises a two-stage combustion process, whereby the bulk of the fuel is burned rich in Stage 1 (to minimise NOx). This is followed by a post-combustion zone where hot unburned ammonia traces reduce the remaining NO. The process is then followed by lean combustion stage (Stage 2), minimising any fuel residue in the exhaust gases.
Read the full report here.
Other news
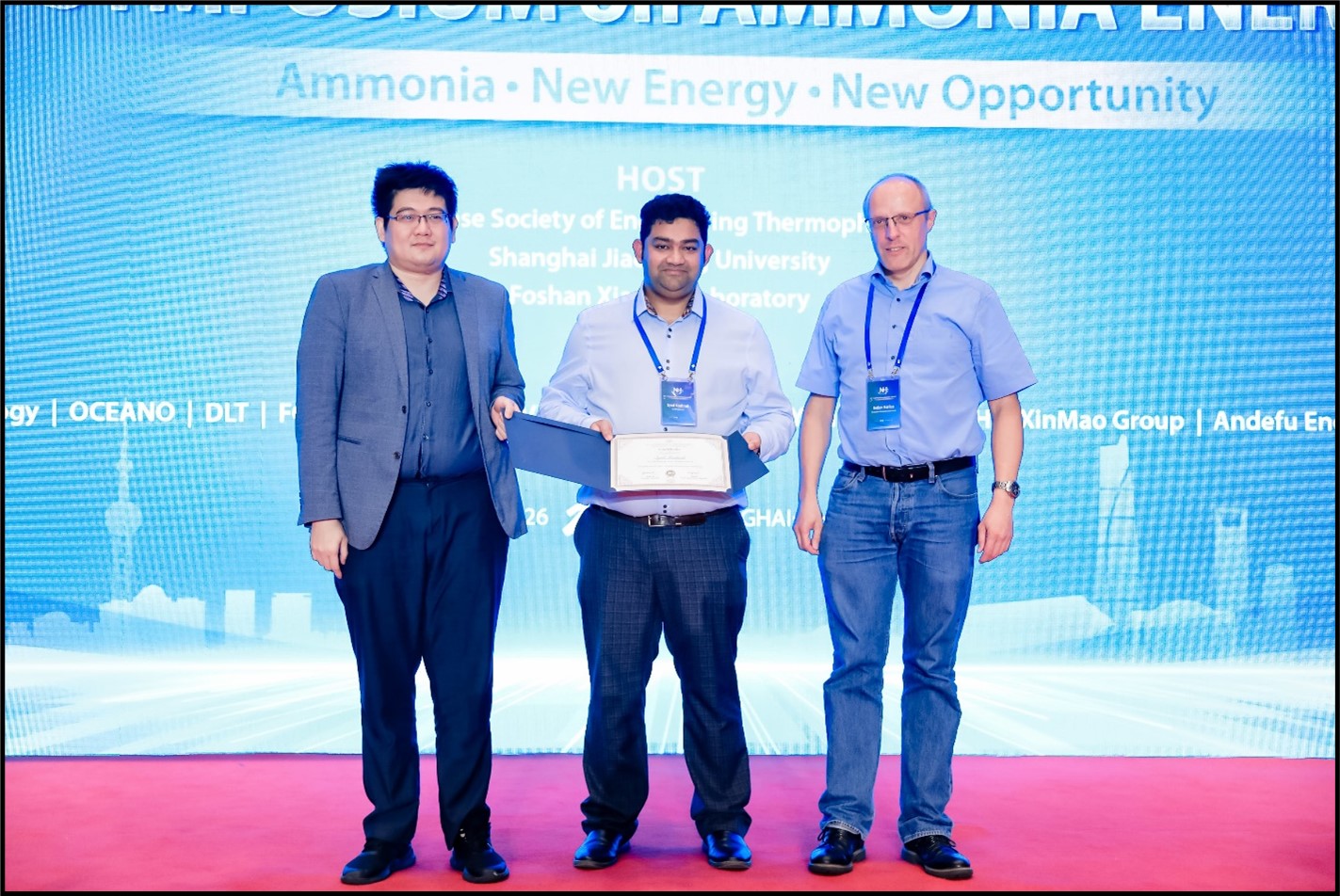
October 2024
The Amburn team from Cardiff University and Flogas Britain recently attended the 3rd International Symposium on Ammonia Energy, in Shanghai, China.
Read more